Smart process control system for the stretch blow molder
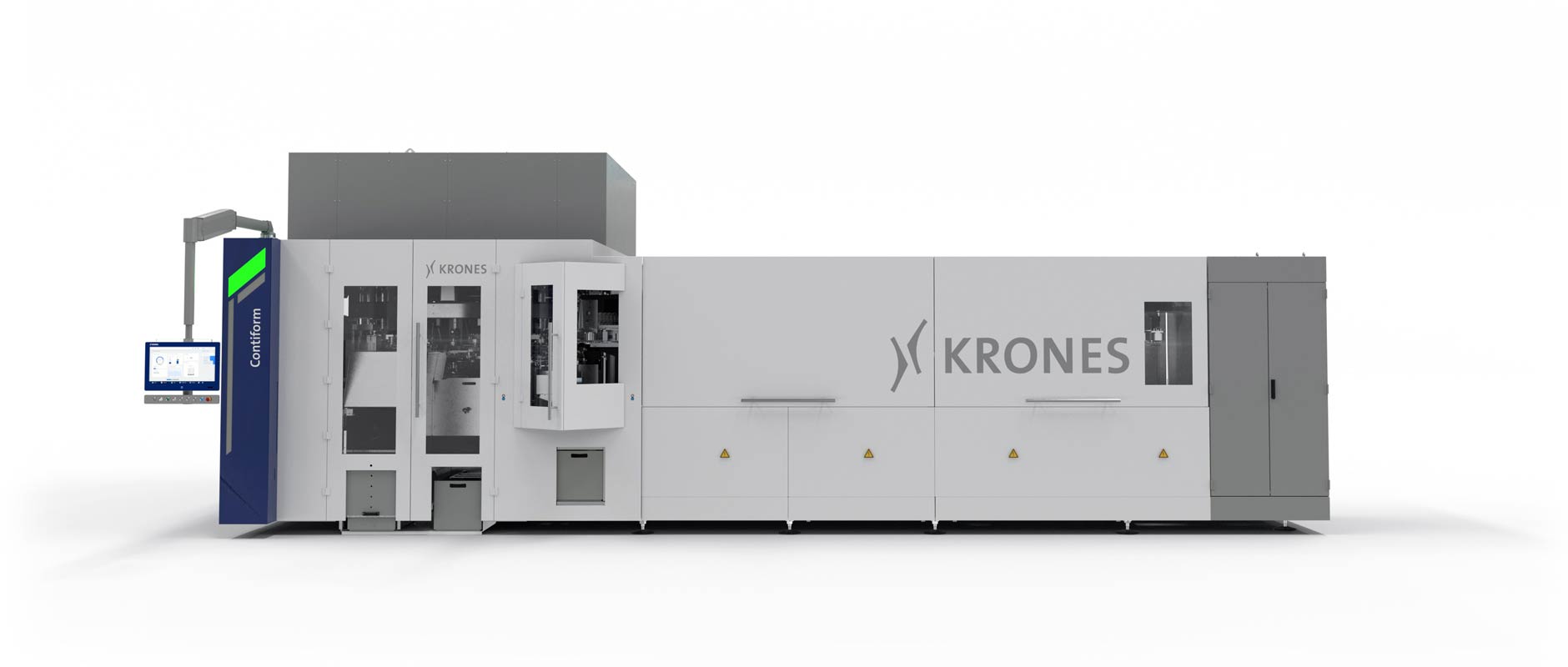
The challenges associated with manufacturing PET containers are varied and complex. Process windows are short, and even the daily changes in ambient temperature and humidity in the production hall require regular manual adjustments to various process parameters to ensure the required level of container quality. Steadily increasing production speeds present another challenge: While the maximum output per blowing station was still at 1,600 containers per hour back in 2000, today’s stations are capable of making up to 2,750 bottles per hour. So, a machine can turn out as many as 100,000 containers per hour. Of course, at such high speeds, even the slightest deviations from ideal conditions can quickly and significantly impact an entire production run.
Meanwhile, demands on personnel are also evolving: State-of-the-art technologies and increasing automation in all areas of filling mean that it takes fewer people to run the machines and ensure successful production. Today, one operator is responsible for multiple machines and systems – and has less time for visual quality checks and manual process control on the stretch blow molder.
Two more important trends must also be borne in mind: First, consumers especially are calling for increased use of recycled PET material (rPET). In order to combine the advantages of PET containers with sustainability, beverage producers must gradually increase the share of rPET in bottles to as much as 100 percent. But not all rPET is created equal. Quality and composition are critical factors – and they can sometimes be rather uneven. Any inconsistencies must be offset in the blow molding process, to ensure that every container meets the specified quality criteria. The second trend is the continued effort among beverage producers to further reduce the weight of their bottles. PET (whether recycled or virgin material) is costly, and high-quality rPET is a scarce commodity. And so it only makes sense to reduce the weight of the containers as much as possible – to save on materials in the production process and to further reduce the containers’ ecological footprint.
Automatic monitoring and smart control of the stretch-blow-molding process
In order to help beverage producers overcome all of these challenges and to provide options beyond manual operator intervention, Krones has developed Contiloop AI.
The system, which is fully integrated into the stretch blow molder, measures the wall thickness of each container at as many as 32 points. During ongoing production, Contiloop AI responds to even the slightest variations in material distribution and automatically adjusts the stretch blow molding process in real time. It also takes into account additional parameters such as ambient temperature and humidity as well as preform feed and discharge temperatures. Any adjustments made are displayed on the HMI to give the operator a clear overview of the current process controls.
Artificial intelligence makes it possible to train and optimize the system
Because production conditions are constantly changing, it’s not enough for Krones to have the controls revert to a specific, pre-set formula. Instead, various initial process settings are made for the system in an automated trial run and the resulting measurements are passed on to the Krones IIoT (Industrial Internet of Things) platform. There, the data flows into the Krones AI pipeline and is used to train the rule algorithm, the “intelligent agent”. When training is complete, the agent is loaded onto the machine’s Contiloop AI and is then available for use in production operations.
Especially worthwhile when processing rPET
In particular, when rPET is used, the available process window is usually very small and can sometimes be more variable than when virgin PET material is used. Even at high speeds and low container weights, this narrow window must be adhered to very precisely. Contiloop AI ensures a very high level of quality in the finished containers and a very low scrap (rejection) rate.
But the myriad advantages of Contiloop AI are not limited to material and process aspects – this ingenious technology also makes work considerably easier for operating personnel. The automated controls mean far fewer manual interventions at the machine, and offline quality assurance can be reduced to a minimum.
Download
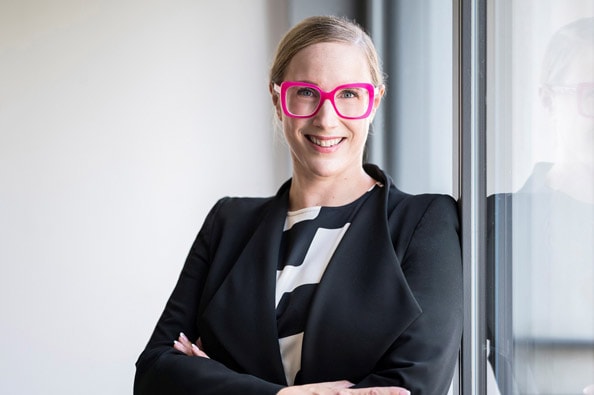
Dr. Anne-Kathrin Bräu
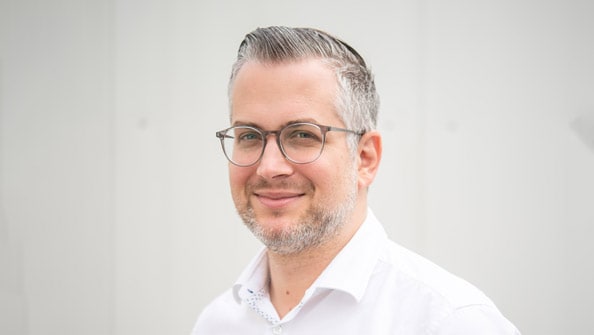
Peter Mörtl