Saving water, CO₂ and more in the brewery, with Steinecker
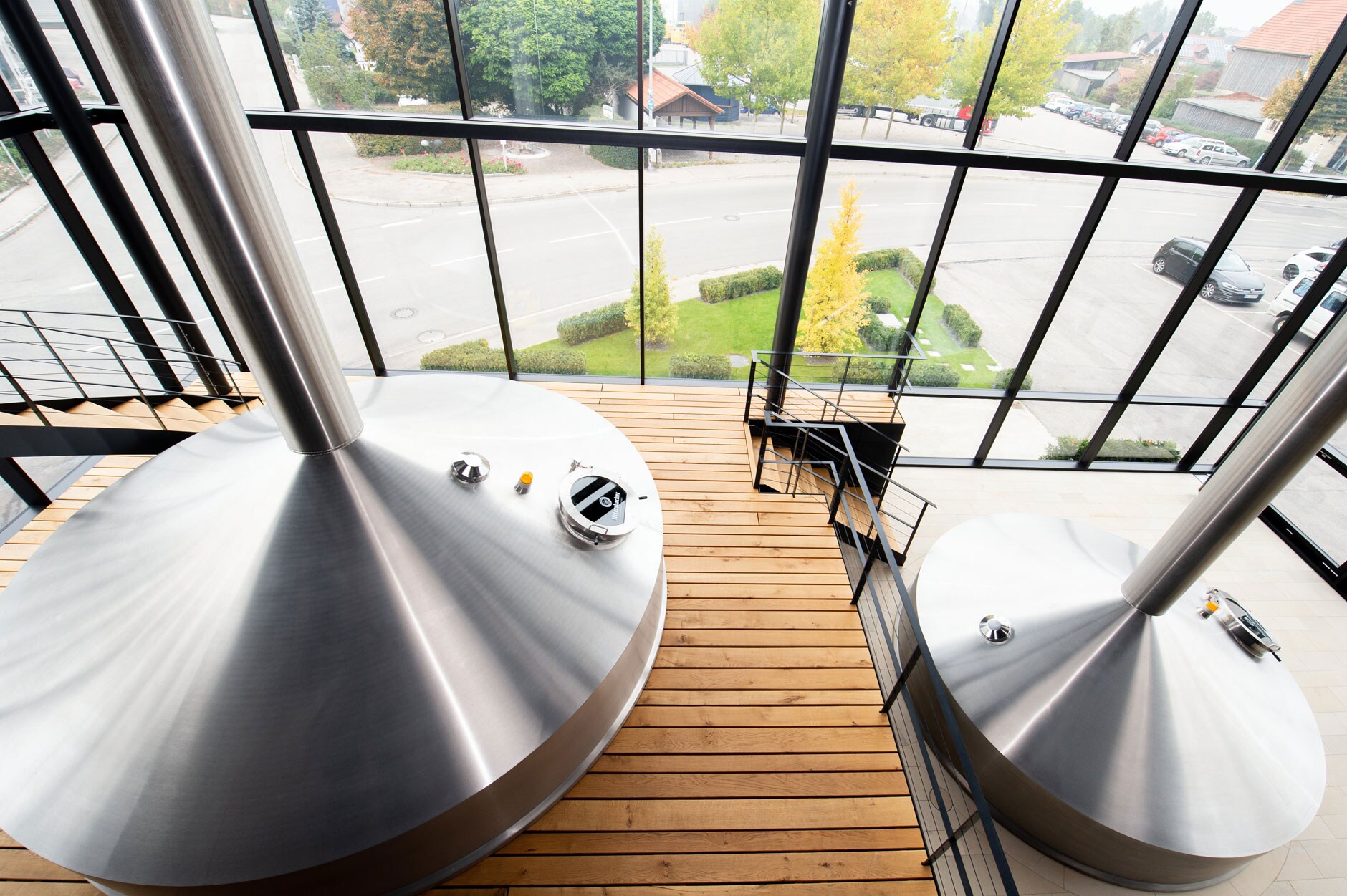
- Steinecker offers a variety of concepts and approaches for creating a sustainable brewing process.
- With Phoenix BMC, breweries can upcycle their residual materials and use them for energy recovery.
- The systematic implementation of a water sustainability concept can significantly reduce water con-sumption.
- Integrating a CO₂ recovery system in-house gives breweries independence from current market condi-tions and increases the sustainability of the production process.
Reducing energy and media consumption is a top concern for breweries. Steinecker has focused its devel-opment efforts on this issue for many years and now offers a solution for sustainable brewing, which goes by the name Brewnomic. By integrating various modules of innovative technologies, efficient energy recovery and resource-economical media supply, breweries can become both energy self-sufficient and carbon neutral. But even using just one or more individual modules from the Brewnomic concept can yield significant savings. At the BrauBeviale 2023, Steinecker is focusing on the topics of water, CO₂ and residuals – presenting suitable solutions for reducing the respective consumption levels and making the most of the valuable constituents of spent grains and yeast.
Upcycling residuals with Phoenix BMC
The Phoenix BMC development project is about upcycling residual materials from brewing and using them for energy recovery. In a new process, Steinecker is able to extract valuable components from spent grains and yeast in the form of a high-quality protein hydrolysate. The first Phoenix BMC module, which executes this process of extracting protein hydrolysate, is currently up and running in a pilot installation at Ustersbacher Brewery. The tradition-steeped Bavarian brewery is committed to becoming an energy-self-sufficient brewery and has for many years now been systematically implementing sustainable solutions from Steinecker.
Total water consumption reduced by half
Water is a precious natural resource and a raw material with enormous potential for savings in the brew-ery. It often takes more than 3.5 hectolitres of water to produce a single hectolitre of saleable beer. With the water sustainability concept from Steinecker, this figure can now be reduced by half. To accomplish this, a brewery that is already working with state-of-the-art equipment from Steinecker simply has to com-bine various modules from the water sustainability concept and adjust its processes. Although it may sound like a daunting task, Steinecker’s experienced team is more than capable of making it reality – and the end result is worth it, for the environment’s sake but also for the brewery’s own ongoing operating costs.
CO₂ recovery ensures production security
As far back as 2005, Steinecker has had CO₂ recovery systems in its portfolio. Particularly in light of the supply chain difficulties and availability issues of the recent past, investing in an in-house plant offers many advantages for breweries. On the one hand, it makes it possible to recover valuable media and to generate synergies with higher-level energy cycles. On the other, it makes the breweries independent of market fluctuations and ultimately ensures production security.
Download
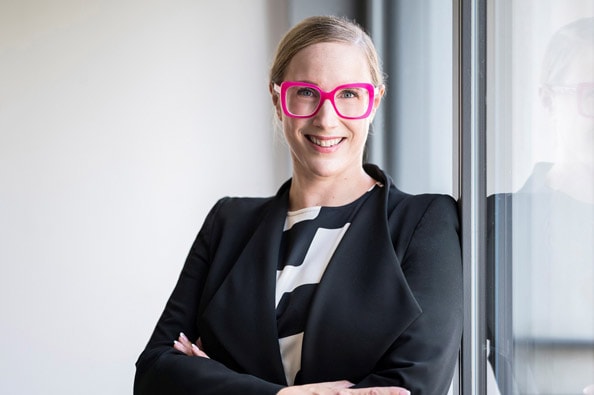
Dr. Anne-Kathrin Bräu
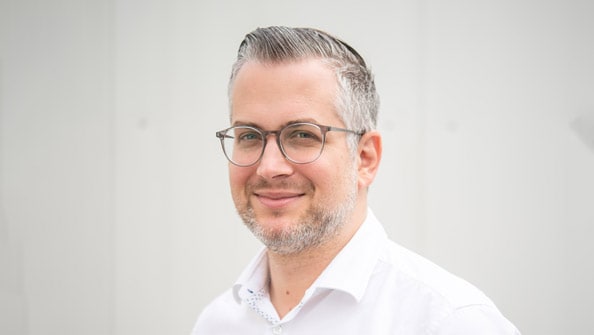
Peter Mörtl